Selecting the Right Heavy Equipment Scrap Attachments
Heavy equipment scrap attachments enable machines like excavators and material handlers to sort, cut, and load scrap.
The right attachment and machine combination will drastically increase a scrap processor’s profits. The wrong combination leads to unnecessary service bills and downtime.
To select the proper heavy equipment attachment, scrap processors should determine the size and weight of the material they are processing and cross reference the machine load chart before renting or purchasing an attachment.
Here is a breakdown of scrap attachments with their functions and best maintenance practices.
Orange Peel Grapples and 2-3 Tine Grapple Scrap Attachments
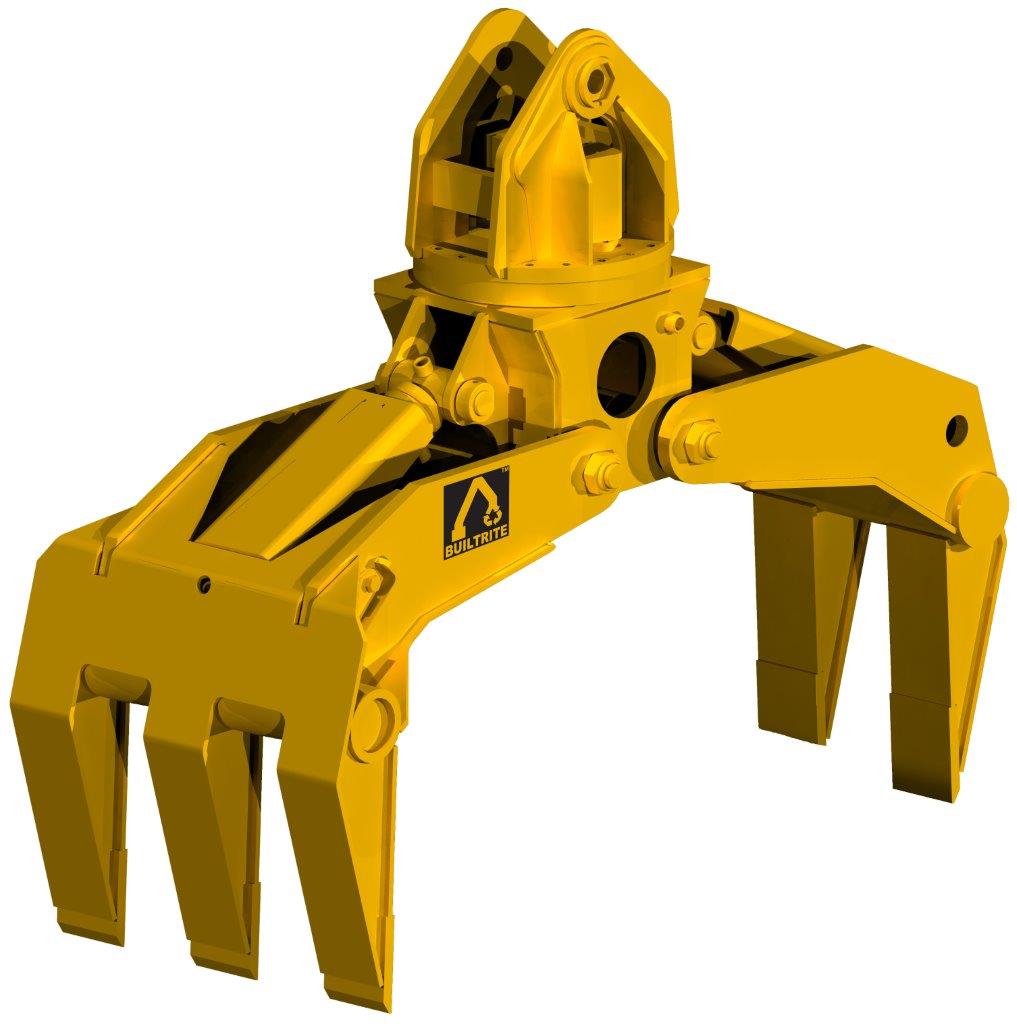
Orange peel grapples are normally used for general material handling and auto hulks. Orange peel grapples are offered with four or five tines.
Some scrap processors really like the four-tine grapples to unload railcars. Others appreciate the five-tine grapple when picking large piles. Ultimately, the decision between a four or five-tine grapple is based on preference in most situations.
An orange peel grapple’s opening width provides a noticeable difference during operation. Orange peel grapples are available in semi-closed, closed, or open configurations. The semi-closed option is the standard configuration for orange peel grapples, and it offers support for most material. The open grapple is ideal for larger, bulkier loads, and the closed grapple is better for handling finer materials.
Another grapple option to consider is the 2-3 tine grapple. This attachment is specifically designed for fast, precise loading of processed auto hulk and baled material. If scrap processors are regularly handling these types of materials, they should consider purchasing a dedicated material handler or excavator with a 2-3 tine grapple for stationary loading of balers and trucks.
Scrap Magnet Attachments
Scrap magnet attachments are regularly used in scrapyards to separate ferrous material from non-ferrous material and unload smaller scrap that no other attachment can grab from truck beds or train cars.
Scrap magnet attachments with more surface area produce a larger magnetic field and pick up more material. Before renting or purchasing a scrap magnet attachment, scrap processors should consider the magnet’s surface area, ampere, the size of their generator in kilowatts, and review their material handler’s load chart.
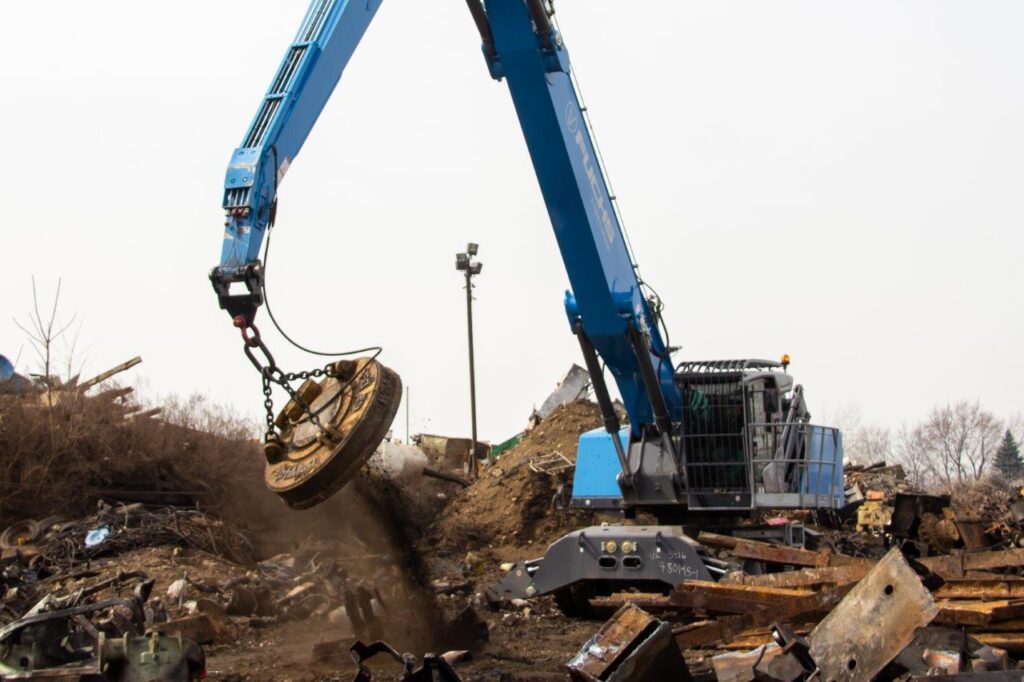
Mobile Shears and Bucket Link Shears
Shears are the go-to scrap attachment when material needs to be resized for further processing.
Scrap processors have the choice between bucket link shears and mobile shears. Bucket link shears offer unmatched cycle times and are more cost-effective than mobile shears. However, bucket link shears have no rotation capabilities, and they cut lighter material than mobile shears.
For example, a LaBounty BLS 2000 can cut a 10-inch I-beam, while an MSD 2000R can cut a 20-inch I-beam. Mobile shears with integrated cylinders, such as LaBounty’s MSD series, rotate so operators can make fewer cuts, reducing wear and tear.
Scrap processors should identify the type of production they need before renting or purchasing a shear.
Material Handlers, Excavators, Skid Steers, or Wheel Loaders
Material handlers are purpose-built for scrapyards because they have higher lifting capacity than excavators and have up to three times faster travel speeds than comparably sized excavators.
Most of the scrap attachments listed above are commonly used with material handlers for these reasons.
However, excavators are better suited for shear operation, and they are more cost-effective than material handlers. If a scrap processor needs a machine to cut scrap or pick up smaller piles with limited travel around the yard, an excavator may be their best option.
While excavators are better suited for shear operation, scrap processors can still employ shears on their material handlers in special circumstances. Material handlers normally feature a straight boom to optimize the machine’s vertical lifting capacity. This type of boom is less than ideal for shearing material at ground level.
To counteract this limitation, some manufacturers offer material handlers with quick coupling systems that allow operators to swap sticks and attach a second member shear. For example, Fuchs offers the Quick Connect (FQC).
“We offer the FQC because there are a number of yards that are pressed for space,” Fuchs North America Sales Manager John Van Ruitenbeek said. “Those scrapyards want one machine that can do more than one function to ensure they are maximizing the potential production capabilities of their space.”
Scrap processors who want shear operation on a material handler can also convert a machine from their fleet. This conversion involves changing the boom configuration to optimize shear operation at ground level.
Other common machines in scrapyards are skid steers and wheel loaders. These machines can be fitted with forks and grapples to transport small and midsize material to shredders or compactors.
Scrap processors should examine their scrapyard layout, material size, and current fleet to determine the need for a skid steer, wheel loader, excavator, or material handler.
Maintenance Guidelines
Understanding proper scrap attachment maintenance is key to the long-term success of a scrap processor. Each attachment has different maintenance requirements. Scrap processors should regularly review these guidelines, which can be found in the operator’s manuals, to reduce downtime and additional costs.
Maintenance for Grapples - Tine Inspections
Orange peel grapples and 2-3 tine grapples require regular tine inspections to examine wear over time.
These inspections will determine if the grapple needs to be shipped to the dealer for hard facing or other maintenance. Without tine inspections, the grapple’s lifting capacity will be affected and catastrophic failure could occur.
Maintenance for Scrap Magnets - Duty Cycles, Daily Inspections, and Proper Storage
Operators should adhere to their scrap magnet’s duty cycles as outlined by the manufacturer.
A duty cycle is the amount of time a scrap magnet can continuously run before needing a break. For example, according to Winkle, its scrap magnets are designed for 75% duty cycles, meaning the magnet can be operated for up to 45 minutes continuously each hour.
If operators do not follow duty cycles as outlined by the manufacturer, the scrap magnet will require costly maintenance or may even need to be replaced.
Operators should also check their scrap magnets before each shift to ensure there are no cracks along the weld seams and that hard facing is still on the pole.
The scrap magnet should be stored on an elevated surface with an air gap to keep the magnet off the ground and avoid damage from moisture. These steps will help avoid significant damage to the machine by identifying minor problems before they become costly service bills.
Maintenance for Shears - Greasing and Welding
The general rule for shear attachments is eight hours of maintenance for every 40 hours of operation. This maintenance could include flipping blades, shimming the blades, building up high wear areas, and reapplying hardfacing. Operators should also grease moving components every four to eight hours.
“If a shear is properly maintained, it can last for decades,” Colby Perkins, Company Wrench’s LaBounty Product Specialist said. “Over nearly two decades, I’ve seen many cases of brand-new shears that are completely useless in a few short months because no preventative maintenance was performed.”
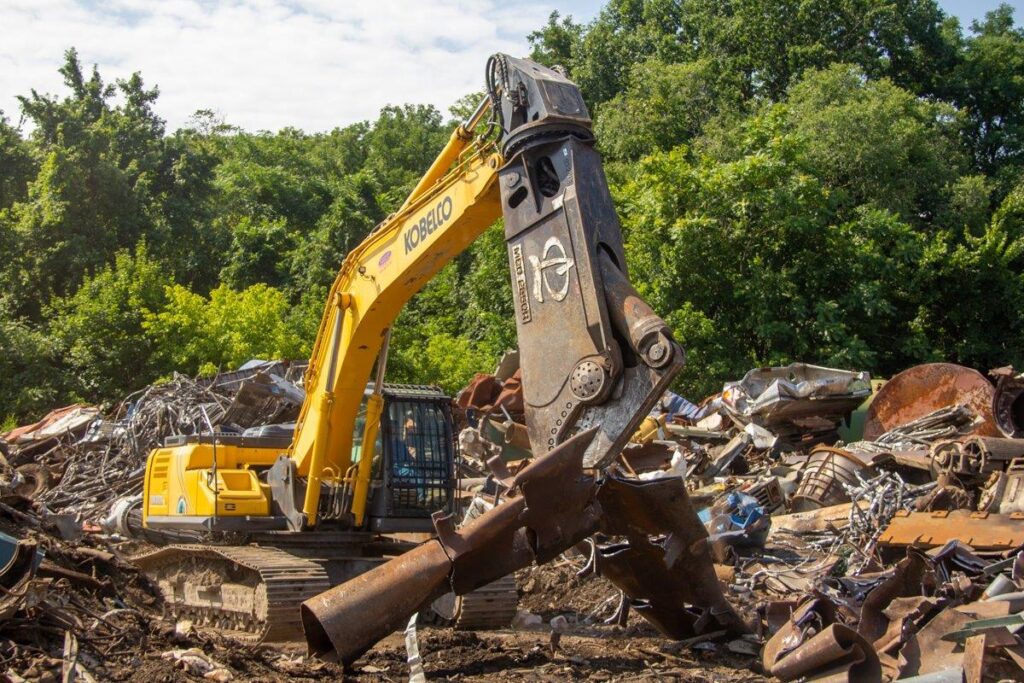
Select the Right Dealer
Scrap processors should rent or purchase attachments from a knowledgeable equipment dealer who specializes in the scrap industry. Some dealers employ experts who can answer any questions related to attachments, including maintenance and operation. Contact your local dealer to learn more about their scrap attachment options.